Step 1
Step 2
Step 3
Plywood board
Plywood comes in the form of sheets with varying thicknesses (approximately 3mm to 30mm), sizes (approximately 6 feet × 4 feet, 8 feet × 4 feet) and grades (waterproof also known as Marine plywood and MR (moisture resistant) also known as a commercial grade). Plywood is engineered wood manufactured by pasting layers of softwood and/or hardwood wood veneers (thin slices of wood) under heat and pressure to create various sizes. The grades of plywood are determined by the type of wood and process used to manufacture them; for instance, hardwood of Gurjan species can be used along with high pressure and temperature pasting method to manufacture the Marine plywood, this is also called the BWP (Boiling waterproof process); whereas commercial plywood can use softwoods such as pine or cedar.
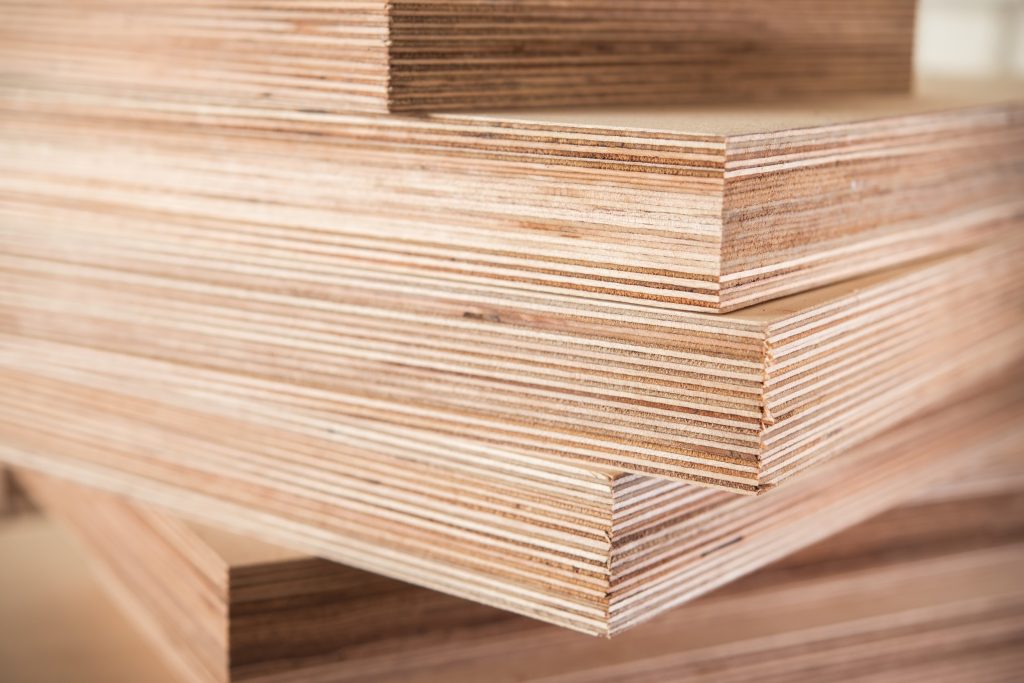
Pros
- High strength and durability
- Good nail and screw holding capacity
- Marine plywood is less susceptible to water damage
- Good termite and borer resistance properties
- Long product life
- Plywood can be made termite resistant and borer free
Cons
- Harder to cut when compared to block boards
- Heavier compared to blockboards
- Unsupported sections above 6 feet tend to bend or sag
- Rough outer finish
- Higher price compared to blockboard
Block board
Blockboards are a form of engineered wood manufactured by gluing wooden battens sandwiched between two layers of veneer, under high temperature and pressure. Just like plywood, block boards come in varying thicknesses (approximately 12mm to 50mm), sizes (approximately 6 feet × 4 feet, 8 feet × 4 feet), and grades (water-resistant also known as Marine block board and MR (moisture resistant) also known as commercial block board). The quality of wood used in the process of manufacturing determines the grade.
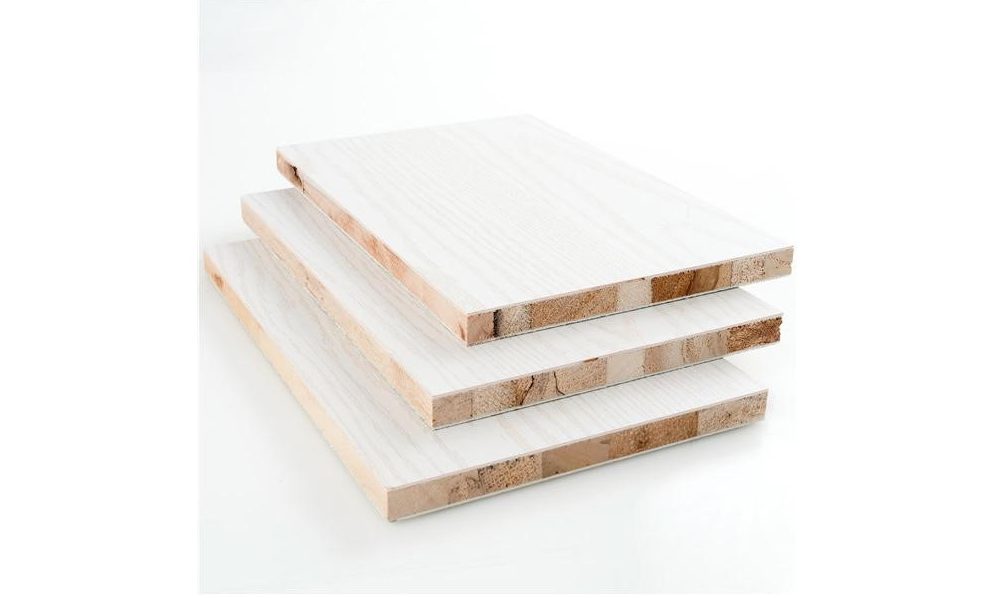
Pros
- Weighs less than plywood
- A good screw holding capacity
- Less prone to bending and sagging
- Workability is easier than plywood
- Lower cost compared to plywood
- Can be made termite resistant and borer free
Cons
- Lesser strength and durability compared to plywood
- Sometimes nails get drawn into the batten gaps and don’t hold well
- More susceptible to water damage compared to plywood
- More susceptible to termites that can be accumulated in the gaps of batten compared to plywood
Particle board
Particleboards or chipboards are engineered wood products made using wooden products like sawmill remains and general wood. These wooden raw materials are first sent to a wood chipping machine to chip them into smaller flakes; these flakes are then filtered to various sizes and mixed with adhesives and resins to form a board. These can be manufactured in many different sizes and thicknesses and are a prevalent option for readymade furniture because of low pricing and good finishing. Although particle boards are not very durable, they can be graded in terms of density.
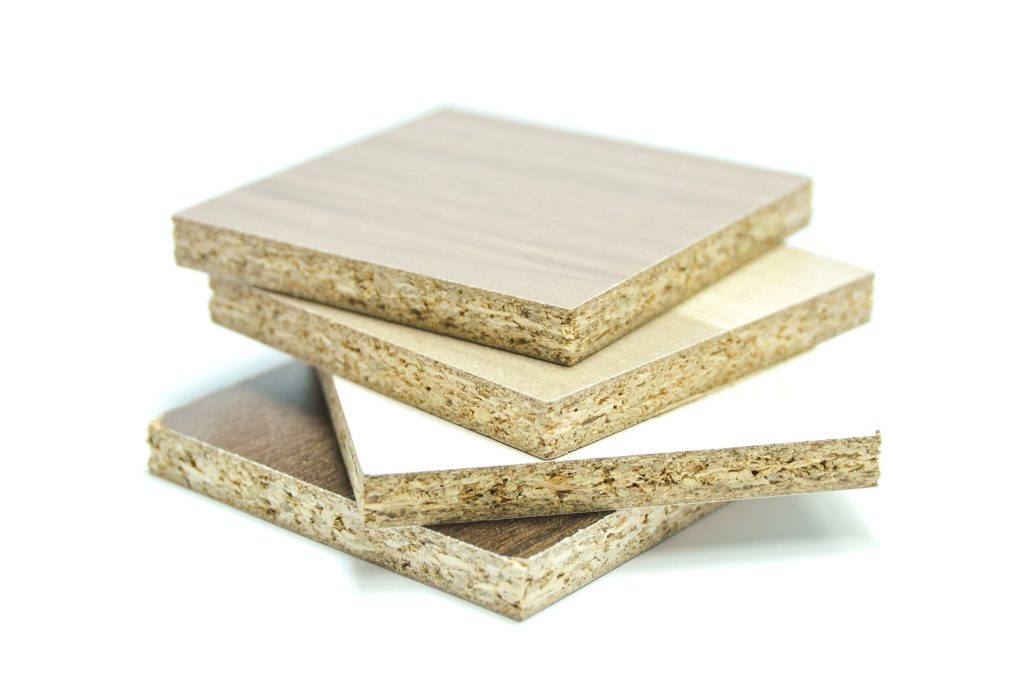
Pros
- Cheapest amongst all options listed here
- Particle boards can be finished with a decorative paper, laminate, membrane, etc
- Lightweight nature makes workability and transportation easy
- They carry good insulation properties
- They are eco-friendly since wooden by-products can be used in their production
Cons
- Perhaps the lowest in strength when compared to other options listed here
- Edges can damage and chip off easily
- Susceptible to decay and disintegration when exposed to moisture and water
- Not good at holding screws and nails
- Not durable
MDF board (Medium Density Fiberboards)
MDF stands for medium-density fiberboards; these are often confused with particle boards. MDF has better physical properties than particle boards; they are stronger, more durable, and have better load taking capacity. The manufacturing process is similar to particle boards with an additional step of finely grinding the wood into sawdust or uniform fibers. These fibers are mixed with adhesives to solidify them and compressed to the desired shape, strength, and size. These are available in various sizes, with the most popular and widely available thickness range is 2mm to 25mm.
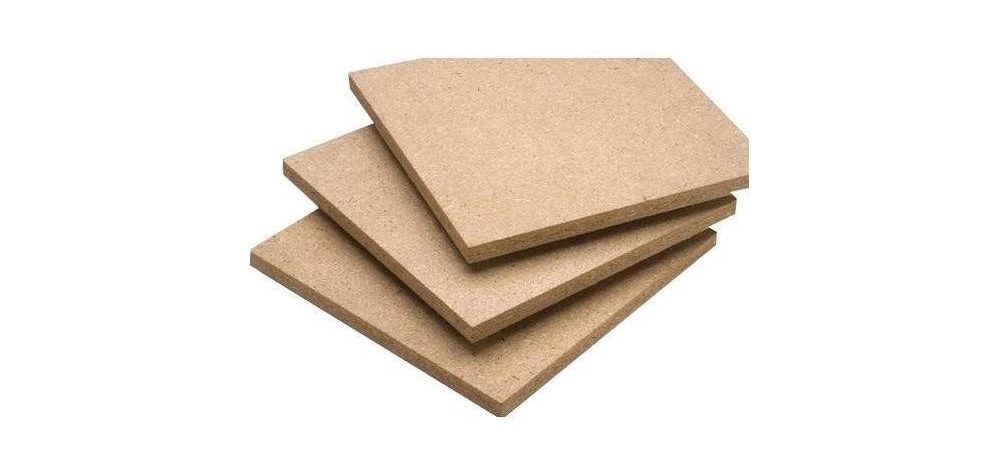
Pros
- Can coat with Duco and PU paint
- Smooth surface finish
- Cheaper than HDF
- Easy workability
- Better strength and durability compared to particle boards
- Termite and borer proof
Cons
- Priced higher compared to MDF
- Non-moisture resistant
- Non-water resistant
- Low density
- Although better than particle board, they still have low nails and screw holding capacity
- Can’t bear heavy loads
HDF board (High Density Fiberboards)
HDF stands for high-density fiberboards; they are denser and stronger versions of MDFs. HDFs are manufactured with almost the same process used to manufacture MDFs except that higher quality raw materials are used along with high pressure and temperatures in the process of manufacturing. HDFs are available in various sizes, but the most popular thickness options are 5mm to 25mm.
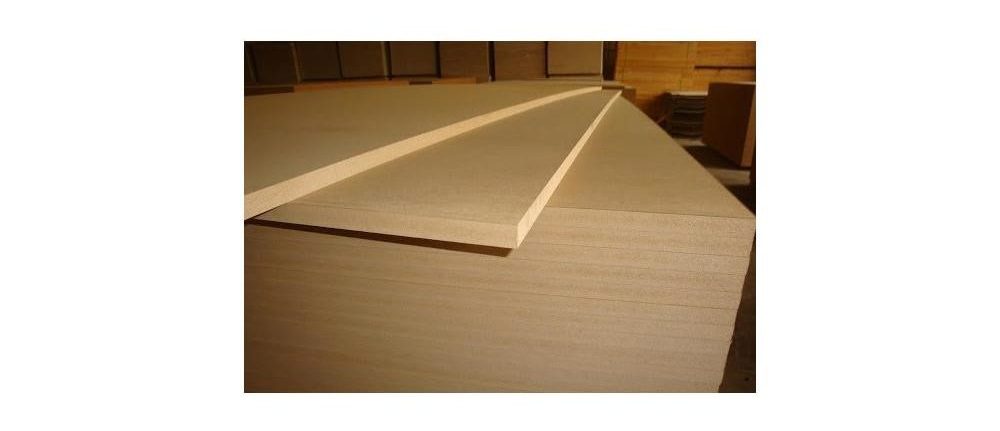
Pros
- Can coat with Duco and PU paint
- Smooth surface finish
- Cheaper than HDF
- Easy workability
- Better strength and durability compared to particle boards
- Termite and borer proof
Cons
- Priced higher compared to MDF
- Non-moisture resistant
- Non-water resistant
- Low density
- Although better than particle board, they still have low nails and screw holding capacity
- Can’t bear heavy loads
HDHMR boards (High density high moisture resistant)
HDHMRs are engineered wood boards just like particle boards, MDFs and HDFs; however, the resins and base materials are of higher composition and quality, which give these boards high density and high moisture resisting properties. In terms of quality, density, weight, and strength, MDFs are superior to particle boards, HDFs are superior to MDFs, and HDHMRs are superior to HDFs. Most of the drawbacks from particle boards, MDFs, and HDFs are overcome by HDHMR. HDHMRs are available in various sizes, but the most popular thickness options are 3mm to 35mm.
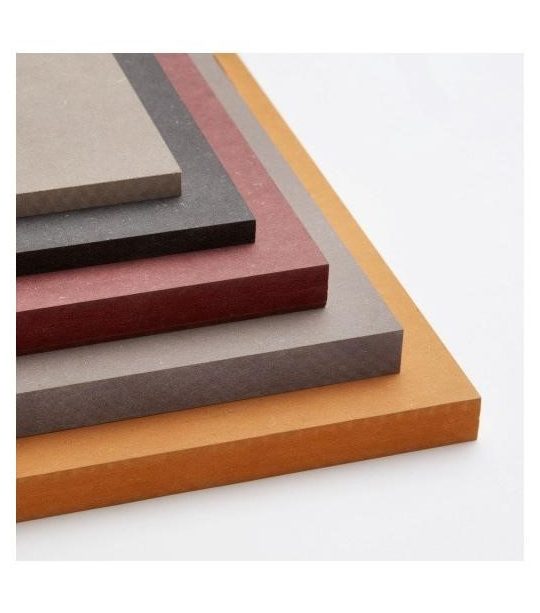
Pros
- Moisture resistant
- Very high termite and borer resistance
- High strength, density, and durability
- Superior surface finishing
- Water-resistant
- Good screw and nail holding capacity
- Termite and borer resistant
Cons
- Costlier than particle boards, MDFs, HDFs
WPC Board (Wood Polymer Composite)
WPC as a material has been available in the market for a very long time, although WPC in the form of boards that can be used to make furniture is slowly gaining popularity because of many advantages they provide. WPCs, as the name suggests, are made of wood and plastic, which are mixed with resins, bonds, and extruded to take the form of boards. These come in various densities that can be generally classified as low, medium, and high density; they are also available in various thicknesses similar to a plywood board.
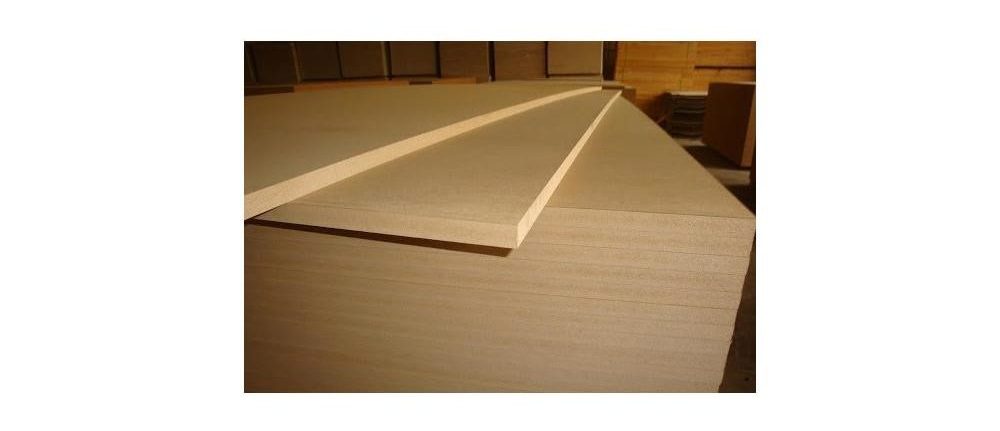
Pros
- High resistance to decay
- High water resistance
- High heat resistance
- Termite proof and borer proof
- High-density boards hold screws and nails well
- Lighter weight compared to plywood
Cons
- Very expensive compared to even the most expensive plywood
Conclusion
- Now that you have already read and understood Plywoods, Blockboards, Particleboards, MDFs, HDFs, HDHMR, and WPCs all of them have their pros and cons. None is better than the other, but each one best outshines the other based on the purpose of use. Keep in mind the installation location, strength, and durability of the material before deciding on the base material purchase to make the right choice and enhance the furniture experience.